喇叭配件的外觀缺陷,如劃痕、臟污、氣泡、變形等,不僅影響美觀,還可能影響喇叭的音質(zhì)和耐用性。傳統(tǒng)的檢測方法依賴于人工檢查,效率低且易受主觀因素影響。流水線視覺檢測設(shè)備能夠?qū)崿F(xiàn)自動化、高精度的檢測,有效提高生產(chǎn)效率和產(chǎn)品質(zhì)量。
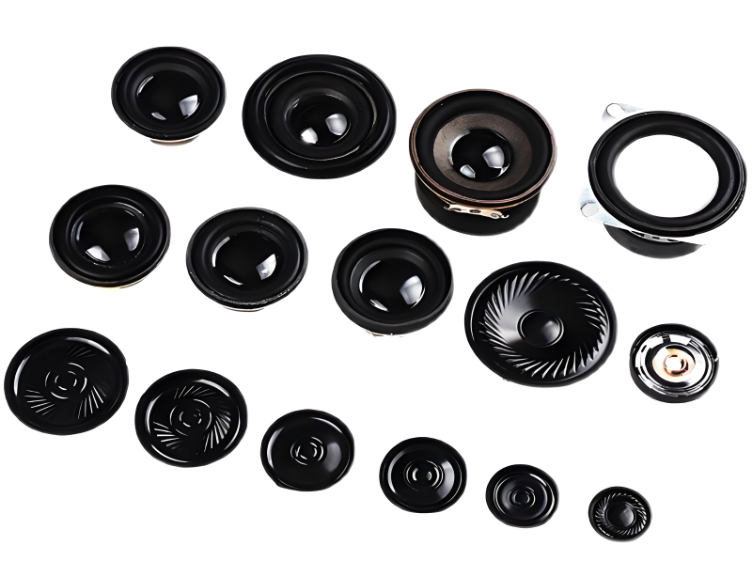
1. 圖像采集:檢測相機捕捉喇叭配件的表面圖像,照明系統(tǒng)提供均勻照明,確保圖像質(zhì)量。
2. 圖像預(yù)處理:對采集到的圖像進行去噪、對比度增強等預(yù)處理,以提高后續(xù)分析的準確性。
3. 缺陷識別:利用圖像處理算法識別喇叭配件表面的外觀缺陷,如劃痕、氣泡、變形等。
4. 尺寸測量:根據(jù)缺陷的特征,通過圖像處理技術(shù)測量缺陷的尺寸,包括長度、寬度、深度等。
5. 結(jié)果判定:系統(tǒng)根據(jù)預(yù)設(shè)的缺陷尺寸標準,對檢測結(jié)果進行判定,輸出合格或不合格信息。
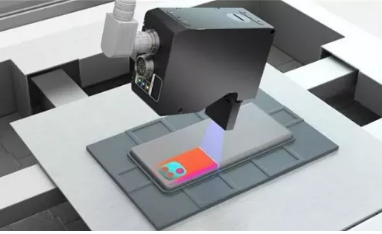
1. 高分辨率相機:用于捕捉喇叭配件的高清圖像。
2. 照明系統(tǒng):包括多種光源,如LED燈、鹵素燈等,以適應(yīng)不同顏色和材質(zhì)的喇叭配件檢測。
3. 圖像采集卡:將相機采集的圖像數(shù)據(jù)傳輸至計算機。
4. 圖像處理軟件:負責圖像預(yù)處理、缺陷識別、尺寸測量和結(jié)果判定。
5. 輸出設(shè)備:如顯示屏、打印機、報警器等,用于顯示檢測結(jié)果和觸發(fā)相應(yīng)動作。
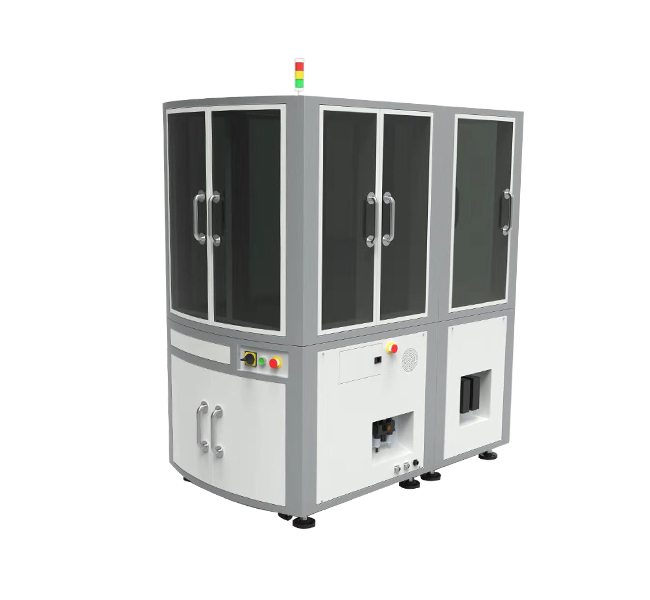
1. 提高檢測效率:流水線視覺檢測設(shè)備可實現(xiàn)24小時不間斷檢測,相比人工檢測,效率提高數(shù)倍。
2. 提升檢測精度:自動化檢測減少了人為誤差,檢測精度更高。
3. 降低生產(chǎn)成本:減少不合格品的產(chǎn)生,降低返工和報廢率,從而降低生產(chǎn)成本。
4. 提高產(chǎn)品質(zhì)量:確保喇叭配件的外觀質(zhì)量和尺寸精度,提高整車性能和用戶體驗。
流水線視覺檢測設(shè)備在喇叭配件外觀缺陷尺寸檢測中的應(yīng)用,實現(xiàn)了自動化、高精度檢測,有效提高了生產(chǎn)效率和產(chǎn)品質(zhì)量。隨著技術(shù)的不斷進步,視覺檢測技術(shù)在汽車制造業(yè)中的應(yīng)用將更加廣泛,為汽車制造業(yè)的智能化發(fā)展提供有力支持。